Operation Headquarters
Bryanston, South Africa
Inhance Solutions
Supply Chain Control Tower, TMS, YMS, and Last Mile Delivery
Italtile Case Study: Transforming Supply Chain Efficiency with Inhance
Italtile Limited, a proudly South African leader in manufacturing, franchising, and retailing tiles and bathroomware, operates across 216 stores in South Africa and the African continent. With a vertically integrated supply chain and a commitment to excellence, Italtile produces 52 million m² of tiles and 2 million pieces of sanitaryware annually. Their focus on sustainability, efficiency, and innovation drives their operational strategy.
CHALLENGE
As Italtile’s market share expanded, so did the complexities of its supply chain. The company faced significant hurdles in optimising deliveries, reducing transport costs, and improving operational efficiency, including:
- Decentralised transport planning resulting in frequent, costly deliveries to the same stores.
- Difficulty in optimising vehicle weight-volume ratios due to a broad product mix.
- Lack of network visibility, making transportation and logistics inefficient.
- The need to enhance sustainability by reducing paper waste and carbon footprint.
SOLUTION
To tackle these challenges, Inhance Supply Chain Solutions developed an Integrated Supply Chain Control Tower Solution tailored for Italtile, providing:
- A fully outsourced 4PL solution, including a dedicated planning team and cutting-edge tools.
- Implementation of TMS Control Tower, Transportation and Load Optimisation Solvers, and Yard Management Solutions.
- Seamless integration with SAP, ensuring real-time data visibility and streamlined operations.
- Flexible and scalable technology applied across manufacturing, distribution, and last-mile delivery.
RESULTS
The collaboration between Italtile and Inhance Supply Chain Solutions has delivered measurable success, driving cost savings, operational efficiency, and sustainability improvements, including:
- Millions of Rands in transport cost savings, achieved through optimised load planning and network efficiencies.
- 98% average weight utilisation, ensuring optimal vehicle space usage and reduced empty kilometres.
- 57% reduction in factory turnaround times, streamlining manufacturing-to-delivery workflows.
- 60% increase in delivery points, enabling Italtile to reach more customers efficiently.
- 30% increase in the transporter base, enhancing logistics capacity and reliability.
- 38% rise in BBBEE SME transporters, promoting supply chain inclusivity and economic development.
- Significant reduction in manual processes and paper waste, contributing to a leaner, eco-friendly operation.
- Optimised delivery routes, reducing carbon emissions and supporting Italtile’s sustainability initiatives.
From Strategy to Success: Quantifiable Benefits and Forward-Looking Insights
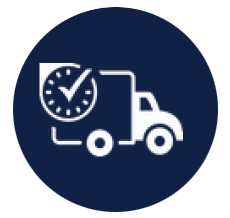
15.5% Increase in on-time delivery
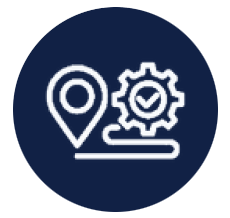
Optimised route planning
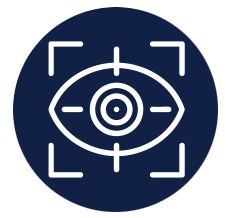
Elevated Transparency in Operations
On-Time Delivery
A 15.5% increase in on-time delivery, ensuring better SLA adherence.
Vehicle Utilisation
A 6% increase in the average vehicle weight utilisation.
Cost Reduction
A 7% reduction in secondary distribution cost per ton.
Enhanced Visibility
Significant improvement in monitoring day-today operations.
Cost Efficiency
Notable savings achieved through optimised route planning.
Service Standardisation
Uniform service levels implemented across various depots, uplifting customer satisfaction metrics.
Data-Driven Decisions
Enabled quick and strategic decision-making through the system’s reporting capabilities.
Strategic Synchronisation
The new system seamlessly aligns with Montego’s growth objectives, mitigating challenges that could scale with the business.
Seasonal Adaptability
Simplified adjustments to high-demand periods.