Supply Chain
Warehouse Management System
Our Warehouse Management System (WMS) is designed to facilitate and improve warehouse operations, offering efficiency, visibility, and control over inventory and processes.
Understanding the Role of a WMS
Managing a warehouse and its operations requires tools that can handle complex tasks. A Warehouse Management System (WMS) serves this purpose. It’s a software solution that aids businesses in the oversight of their warehouse from goods arrival to dispatch.
With a WMS, you can:
- Monitor warehouse operations in real-time
- Handle tasks that previously required manual labour and extensive paperwork
- Gain a comprehensive view of the entire warehouse process
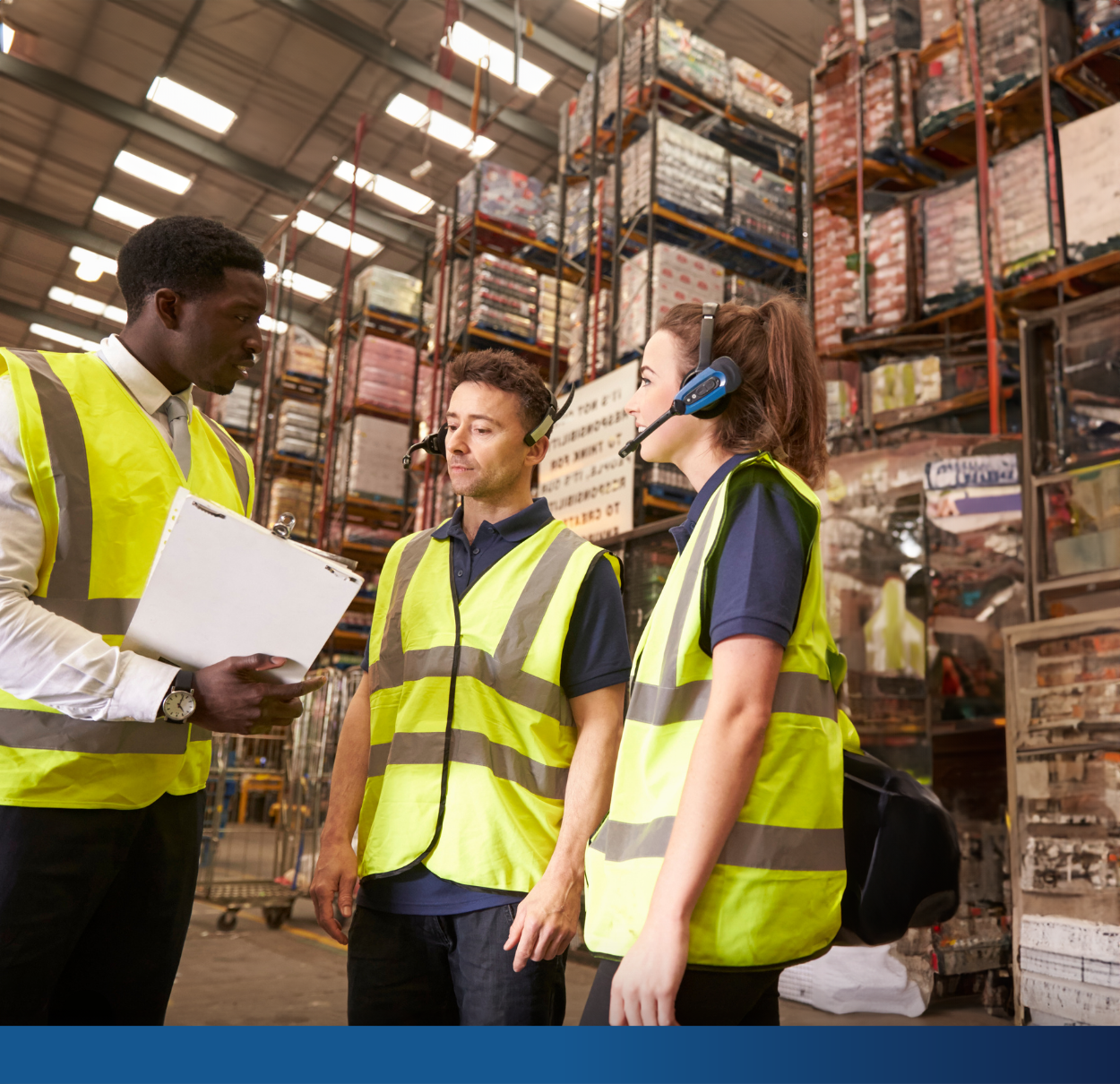
Introducing Inhance’s WMS: Your Gateway to Streamlined Operations
Simplify the complexities of warehouse management with Inhance’s WMS. Revel in the synergy of streamlined operations and a robust distribution centre, armed with tools crafted for excellence. Dive into a world where automation takes the forefront, and efficiency becomes the standard.
Our WMS solution supports all Key Warehousing Functions:
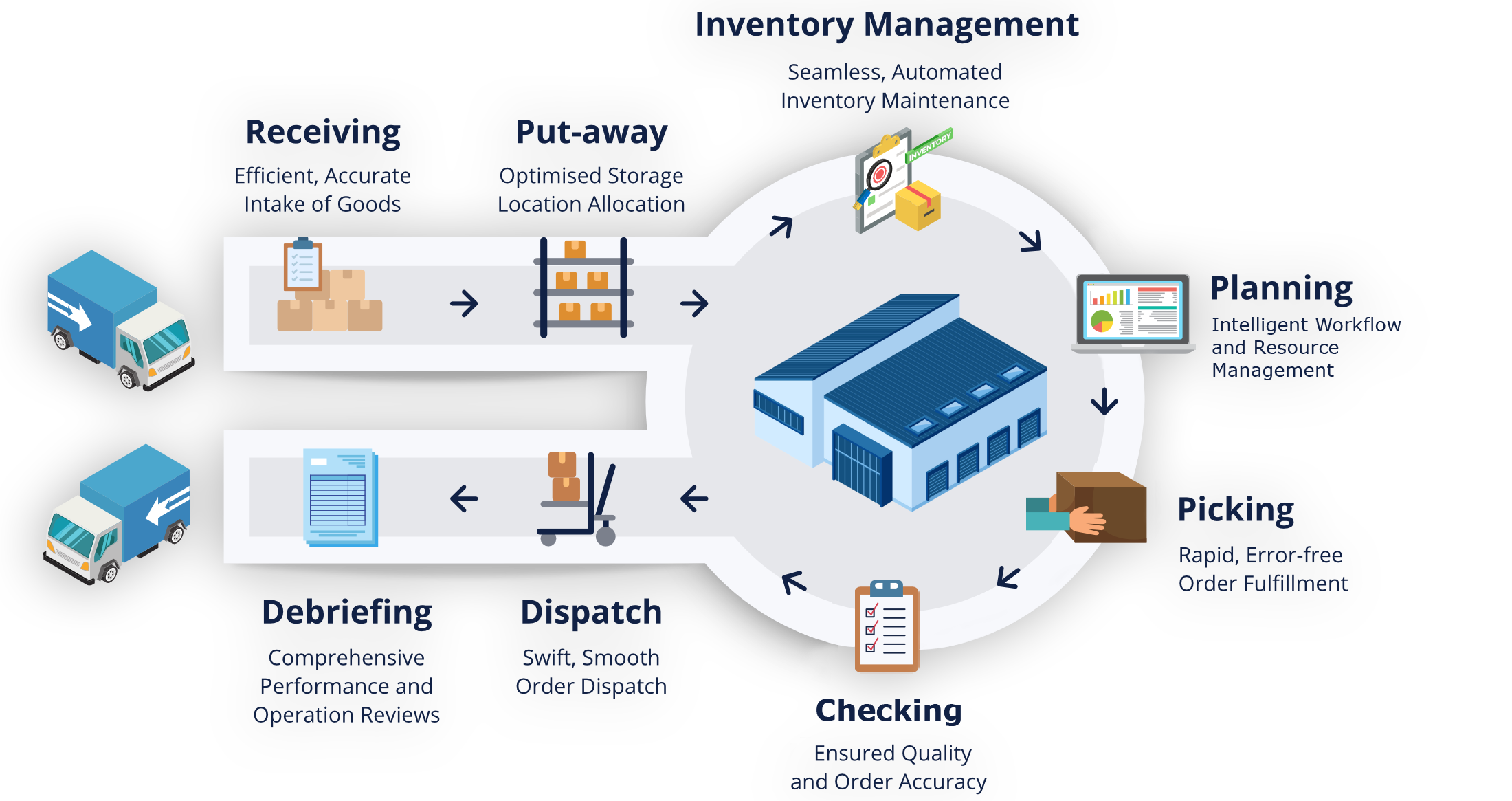
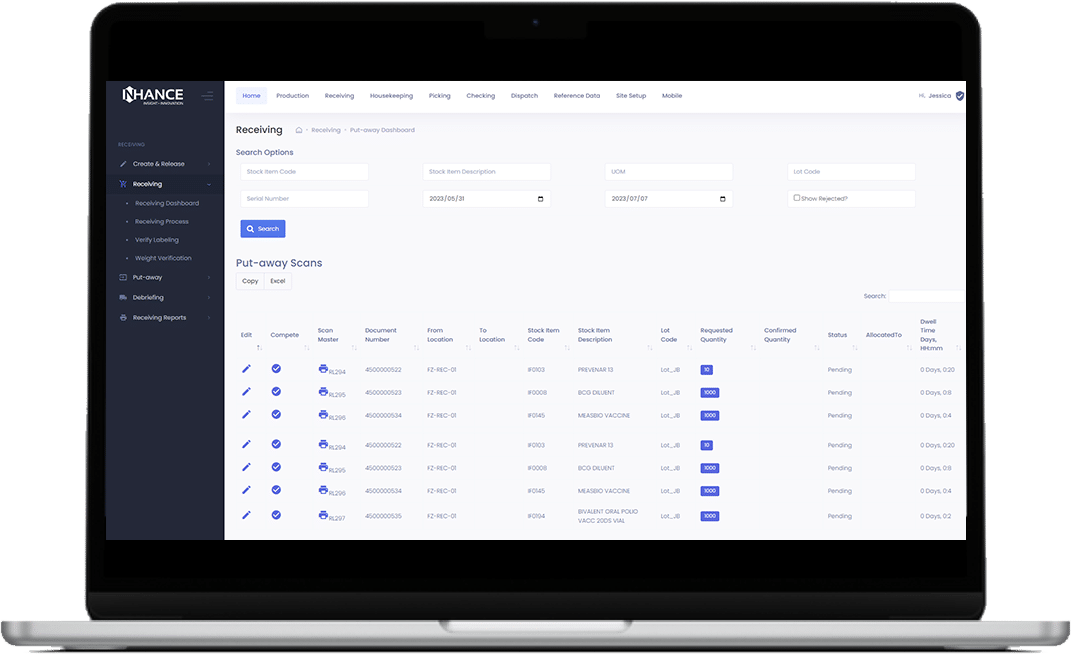
Receiving
Guided by inbound instructions, we record product specifics and prepare stock for put-away via uniquely assigned pallets, streamlining warehouse operations.
Supported Features:
- Multiple deliveries against an original order
- Planned & Unplanned returns
- Receiving into selected receiving locations / bays
- Records Vehicle, Delivery Note and related information
- Restricted over-receipt rules
- Batch registration & expiry dates
- Extracting of samples for products that require samples to be taken
- Labelling - e.g. Product, Carton, Pallet
- Recording of damages
- Importing of documentation
- Receiving by any defined pack unit of measure – e.g. unit, case, pallet
- E-mailing of GRV once receiving has been completed
- Building of put away jobs – full (single sku) & mixed (multiple sku’
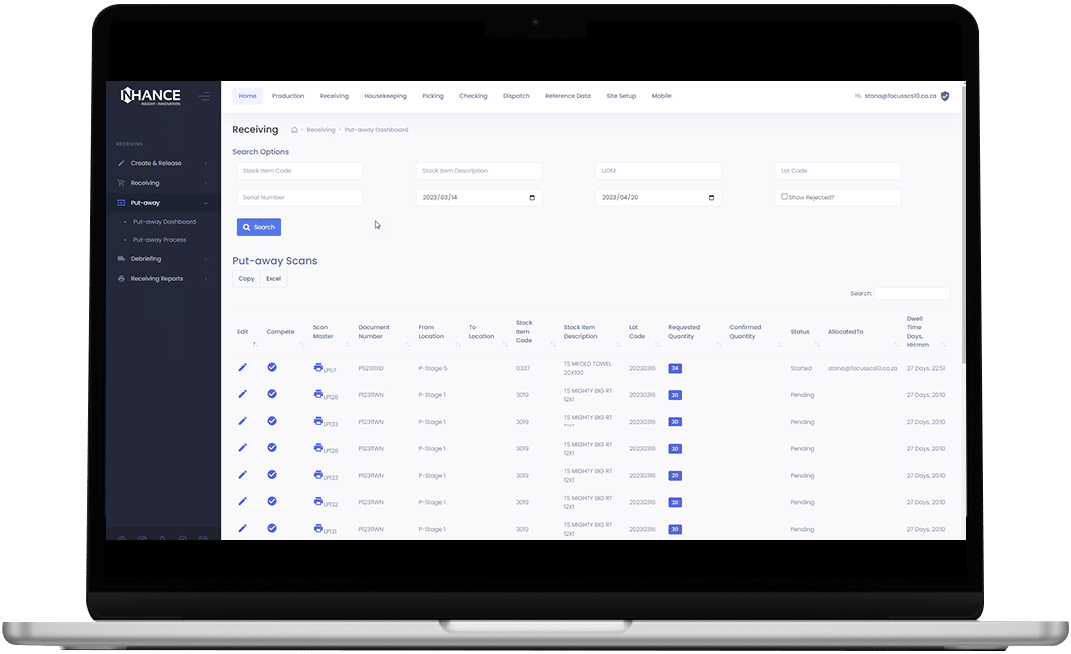
Put-away
Our system manages and oversees the entire put-away process, ensuring structured and efficient operations.
Supported Features:
- Put-away assignments/pallets are staged for put-away
- Each put-away pallet has a unique number plate which will initiate and guide the put-away process
- Real-time visibility of how long stock is staged before being put away
- Urgent stock is prioritised for put away
- Cross-dock stock is taken to a cross-dock staging area
- System-guided slotting
- Put-away is done using RF scanning
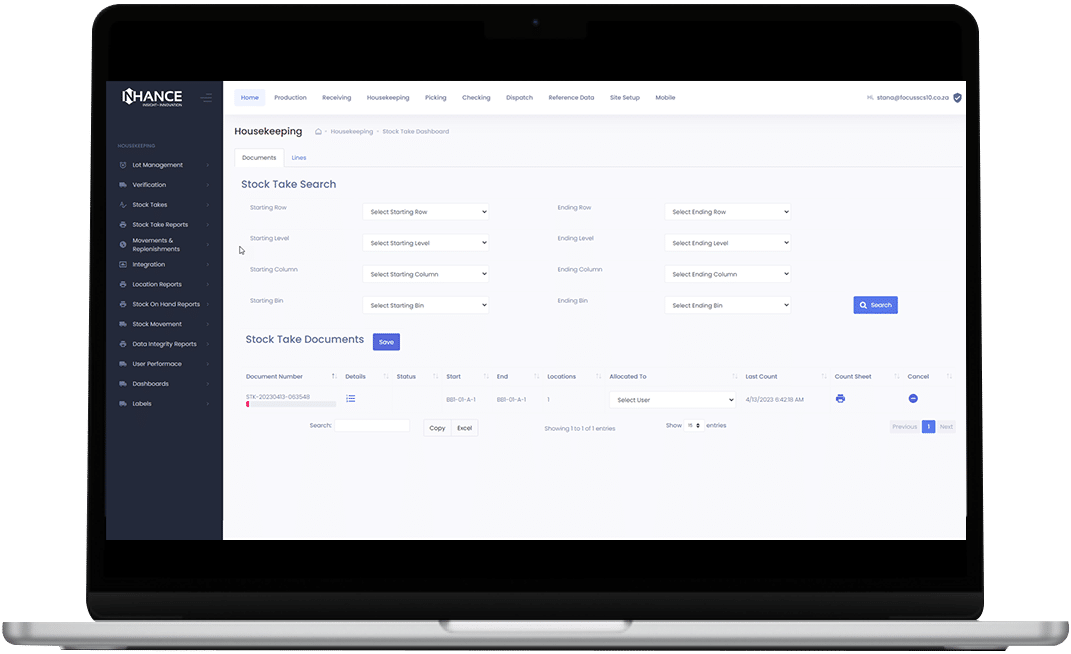
Inventory Management
Inventory Management entails comprehensive tasks like stock control, location management, and efficient task allocation based on operator priorities.
Supported Features:
- Allocation of product to a store location
- System-directed put-away
- Allocation of put away task to a user group
- 2 Stage put away from receiving
- Pick bin setup and health checks
- Movements – done via RF scanners
- Replenishments from bulk to pick bins which are generated by the system based on defined min / max quantities
- Role-based allocation of work
- Operators are linked to areas/zones and are allocated tasks for those areas
- Depending on resource requirements an entire operator group does not have to be allocated a task type priority but instead, this can be done by named operator
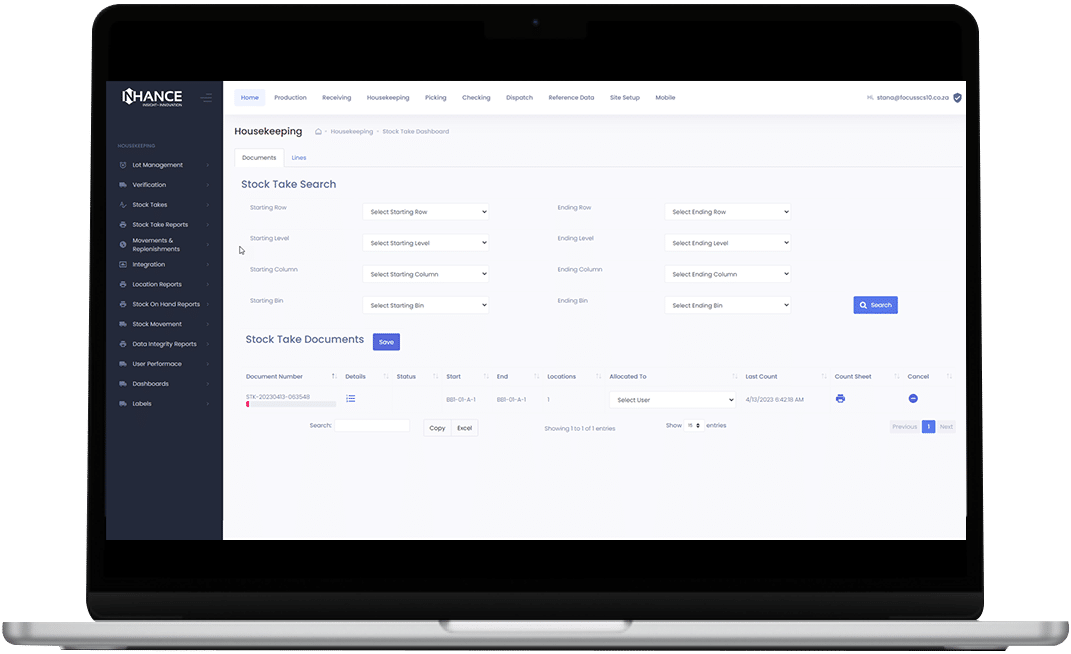
Planning
We facilitate varied planning strategies, releasing tasks based on your unique business type and operational needs.
Supported Features:
- Planning outbound documents based on priorities
- Splitting pick jobs between different areas within the warehouse
- Outbound order delivery date management
- Managing the floor workload based on the number of orders released for picking
- Linking multiple outbound orders to a shipment to ensure picking efficiencies (bulk pick)
- Allocation of stock to pick location
- Allocation of batches based on FEFO
- Dashboard views of workload to be completed within specified cut-offs
- Build pick jobs – the system automatically builds the picks based on the system parameters that are se
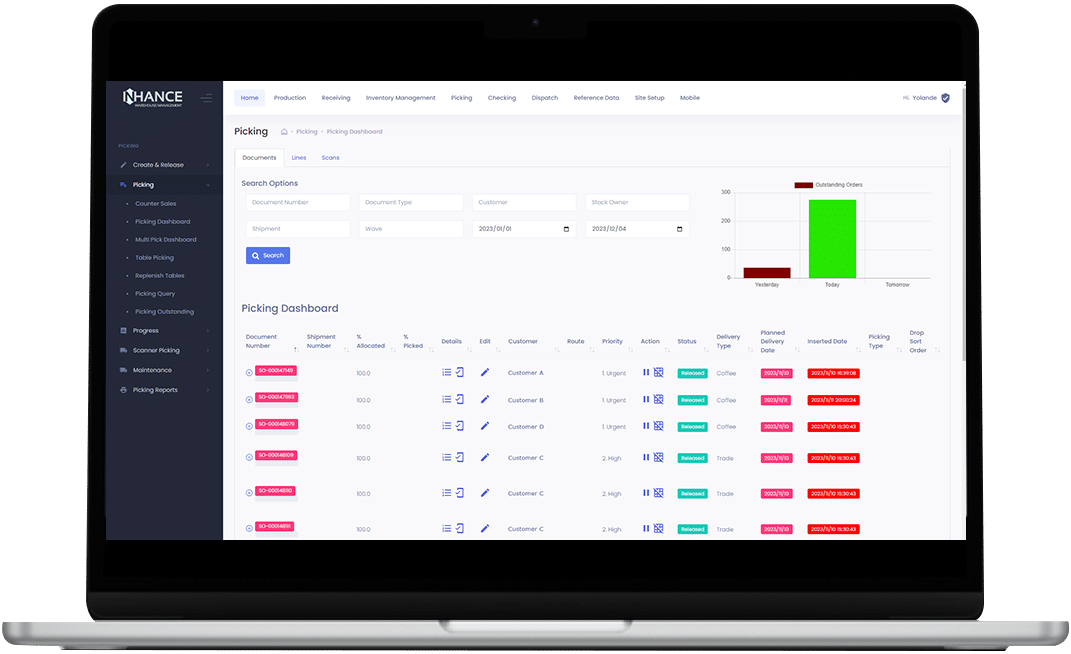
Picking
Our system efficiently organises pick instructions, prioritising tasks for pickers either from the queue or via specific job allocations.
Supported Features:
- Full pick from bulk storage
- Partial pick from the pick face
- Managing the pick job (status tracking)
- Pausing of picking jobs
- Reissuing of short picks before completing picking process
- Exception stock counts
- Automated redirection to alternative locations in the case of a short pick
- Confirmation of batch number on pick job
- Allocation of pick jobs to the correct user group
- Consolidating outbound shipment into a selected dispatch location
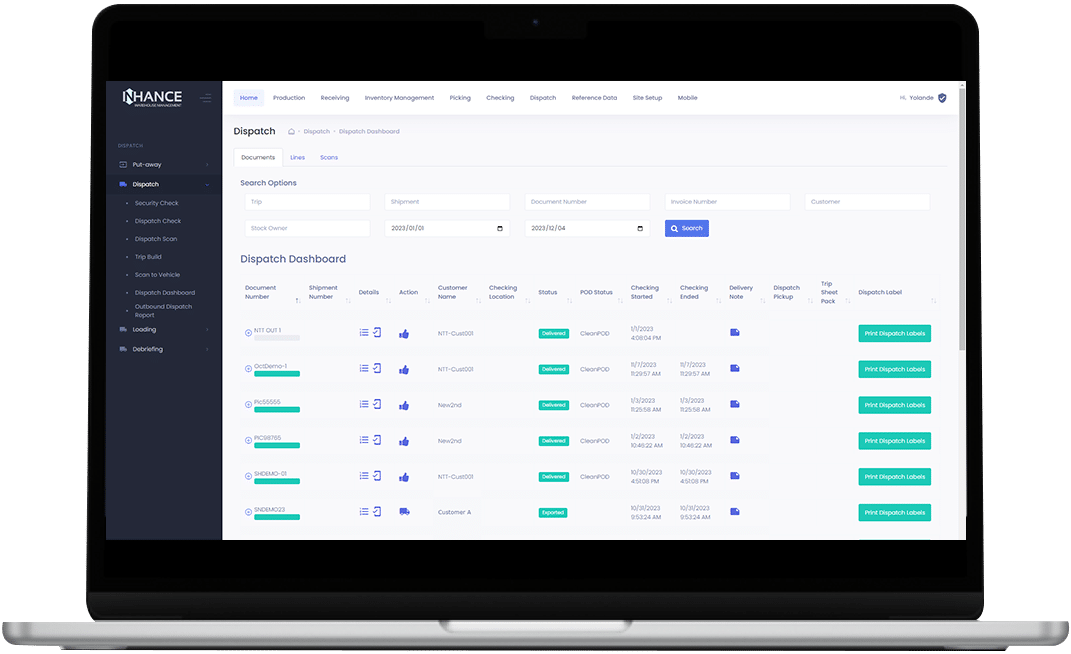
Dispatch
Our system ensures a thorough dispatch process, facilitating stock scanning, route status tracking, and load building. It emphasises accountability, allowing trip closure and document printing only after all packages are confirmed loaded.
Supported Features:
- Scan and confirm stock into Dispatch
- Scan and confirm to vehicle
- Dashboard views that display all routes & the status of orders staged for the routes
- Scanning handover between Checking and Dispatch
- Staging in Dispatch
- Building of Loads / Trips
- Trips cannot be closed until all packages have been scanned ensuring that no stock is left behind
- Dispatch documentation pack can only be printed once the vehicle has been loaded and the trip has been closed
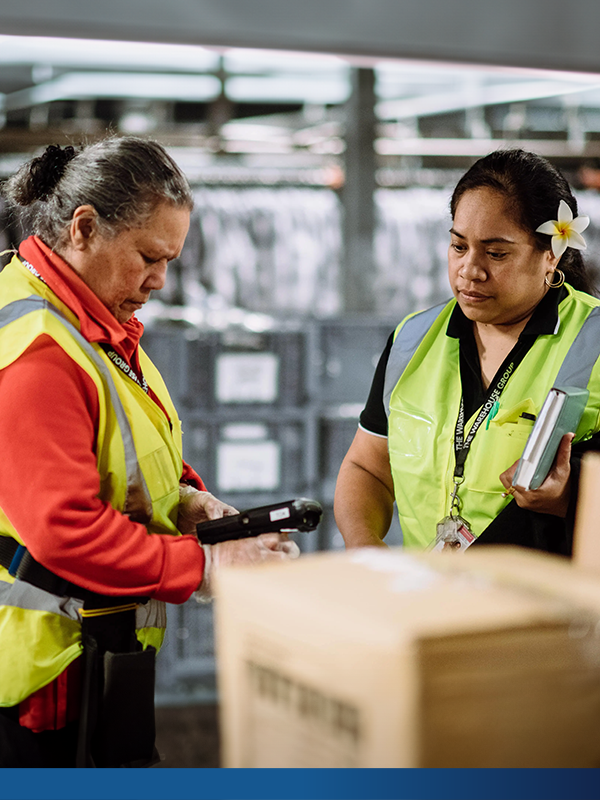
Debriefing
Upon warehouse return, drivers must submit any remaining vehicle stock and provide signed proof-of delivery documents, ensuring full accountability and transparency.
Supported Features:
- Hand POD’s to warehouse
- Receive planned Customer Returns
- Receive stock that was not delivered (placing the order back into dispatch status). Or stock from a rejected delivery (may be changed to be re-delivered)
- Create a Credit note on the WMS for unplanned returns and receive the stock against the WMS document with the appropriate reason codes
- Damages in-transit
- Lost in-transit
- Incorrect customer
Key Features
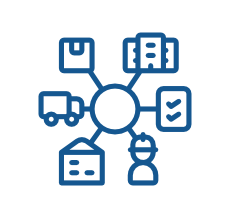
Advanced Inventory Management
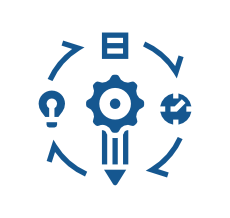
Automation & Workflow Management
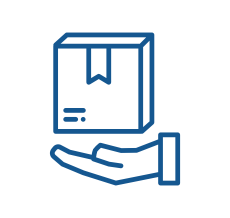
Electronic Receiving & Put-away
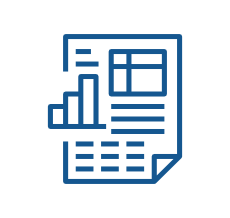
Advanced Dashboarding & Analytics
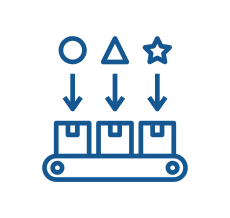
Robust Order Fulfillment Strategies
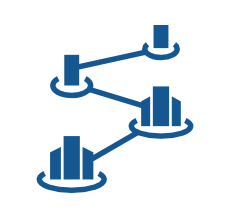
Scalable Architecture
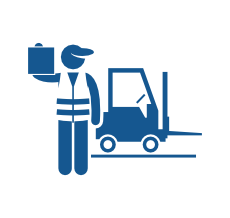
Optimised Picking and Packing
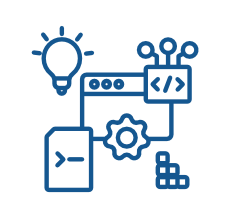
Seamless Integration Capabilities
The Inhance Edge: A Wealth of Benefits
By adopting Inhance’s WMS, you can expect streamlined operations, real-time inventory visibility, improved workforce productivity, reduced operational costs, and a high ROI.
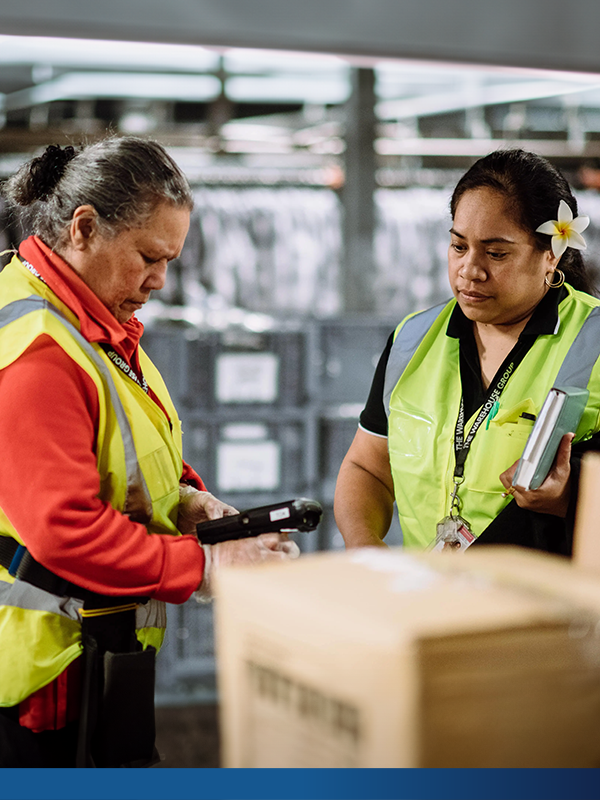
Optimised Inventory Control
Gain real-time accuracy and visibility of your inventory, boosting your planning capabilities and reducing risks of stockouts or overstocking. With full batch traceability and sophisticated shelf life management, maintain superior control over your products’ lifecycles. This empowers you to make informed decisions and deliver accurate, timely information to your customers.
Significant Cost Savings
Our WMS delivers significant cost savings by improving efficiency, accuracy, and visibility in your warehouse operations, reducing costs associated with labour, inventory holding, lost or damaged stock, and inefficient processes.
Streamlined Warehouse Operations
Our WMS automates and optimises key warehouse processes from receiving to shipping. Enhance speed, reduce errors, and save costs while improving your overall customer service.
Effective Labor Management
Track worker performance, optimally schedule tasks, and balance workloads to boost productivity and cut labour costs. Safeguard your staff by directing them along optimal routes within your warehouse.
Informed Decision Making
Leverage the data generated by our WMS for insightful analytics and reporting. Make strategic decisions based on throughput times, labour efficiency, or inventory turnover, and proactively address potential issues.
Seamless Scalability
Our WMS grows with your business. Effortlessly accommodate increased volume, additional SKUs, or more complex operations without a drop in efficiency or accuracy.
Improved Customer Service
Increase operational efficiency and accuracy to significantly improve customer service. Process orders faster and with higher accuracy, resulting in quicker delivery times, fewer errors, and enhanced customer satisfaction.
Let’s optimise, automate and improve your warehouse.
Talk with an expert to learn more about Inhance’s Technology.