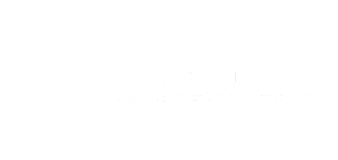
Weldamax: Turbocharging Warehouse Efficiency with Inhance WMS
Operation Headquarters:
Boksburg, South Africa
Industry:
Gas and Welding Products
Inhance Solution:
Warehouse Management System
Overview
Unique Welding is South Africa’s leading independent distributor of gas and welding products, renowned for its innovation and specialised services. With global partnerships, the company offers an unparalleled range of welding equipment, gases, and associated products across multiple fields. Their dedicated team and nationwide service centres provide unmatched after-sales support. With an efficient supply chain that extends throughout South Africa and into its southern regions, Unique Welding is committed to personalised customer engagement rather than impersonal call centres, making them an agile and customer-focused organisation.
The Challenge
Navigating the Complex Labyrinth of a Sprawling Warehouse
Managing a warehouse that sprawls over 4,000 square meters and contains 5,000 distinct locations is no small feat. For Weldamax, a leading distributor of gas and welding products, this complexity had started to erode operational efficiency. Faced with spiralling issues in inventory management, order fulfilment, and stock allocation, Weldamax needed a robust solution.
Key Pain Points:
Low throughput
Inefficient visibility over orders
Error-prone processes
Ineffective stock allocation
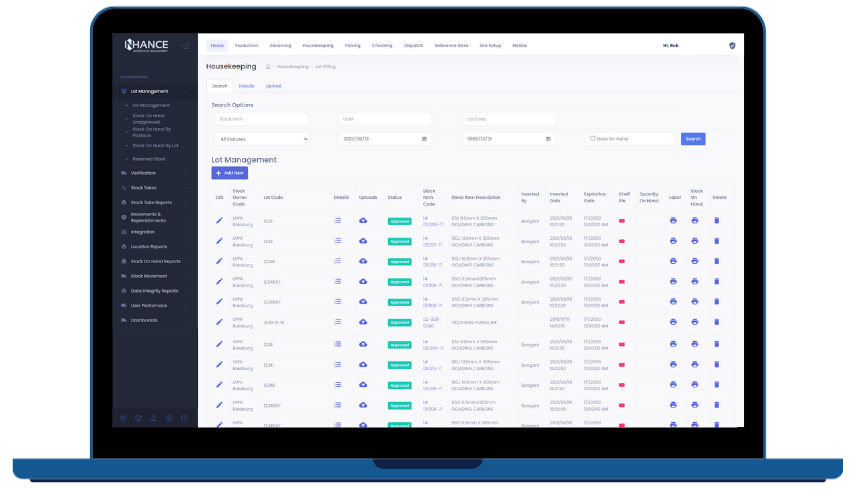
The Solution
Tailoring Precision with Inhance WMS
Understanding the uniqueness of Weldamax’s challenges, we deployed our cloud-based Warehouse Management System, tailored specifically to their needs. Our comprehensive platform covered all the bases: from receiving and put-away, through to planning, picking, checking, and dispatch. Weldamax found a seamless way to manage everything—be it components, consumables, or complex machinery.
The Results
A Quantum Leap in Operational Excellence
In just a short span of three months, the improvements were nothing short of staggering.
Enhanced Operational Speed and Efficiency
Improved throughput and better visibility of orders facilitated meeting defined cut-off times with greater efficacy.
Minimised Errors and Returns
Warehouse-related errors plummeted, reducing returns and credits by an astonishing 99%.
Efficient Stock Allocation
A streamlined process enabled effective stock allocation to orders, back-orders, and key clients, adding value across the board.
“I have been involved in multiple system implementations, and Inhance WMS was by far the easiest, seamless implementation with minor snags that were resolved faster than expected. Inhance WMS has given my team and me visibility and control over all operational aspects and helps me provide the best possible customer service. The Inhance WMS team were easy to engage with and easily understood our requirements. I would recommend Inhance WMS to any organisation.”
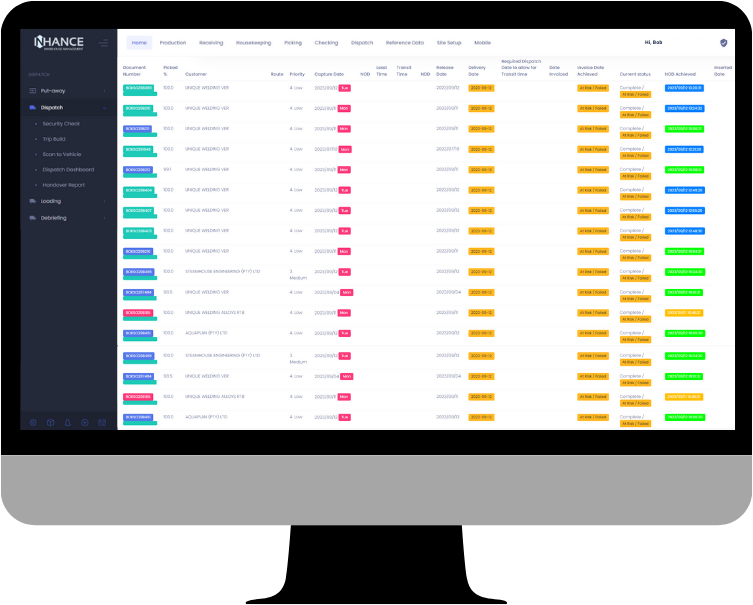